Reassembly of actuator, 35m reverse acting actuator atc (air to close), Trouble shooting – LowFlow Mark 708HP Series 8000 psi Control Valve User Manual
Page 4: Ordering spare parts
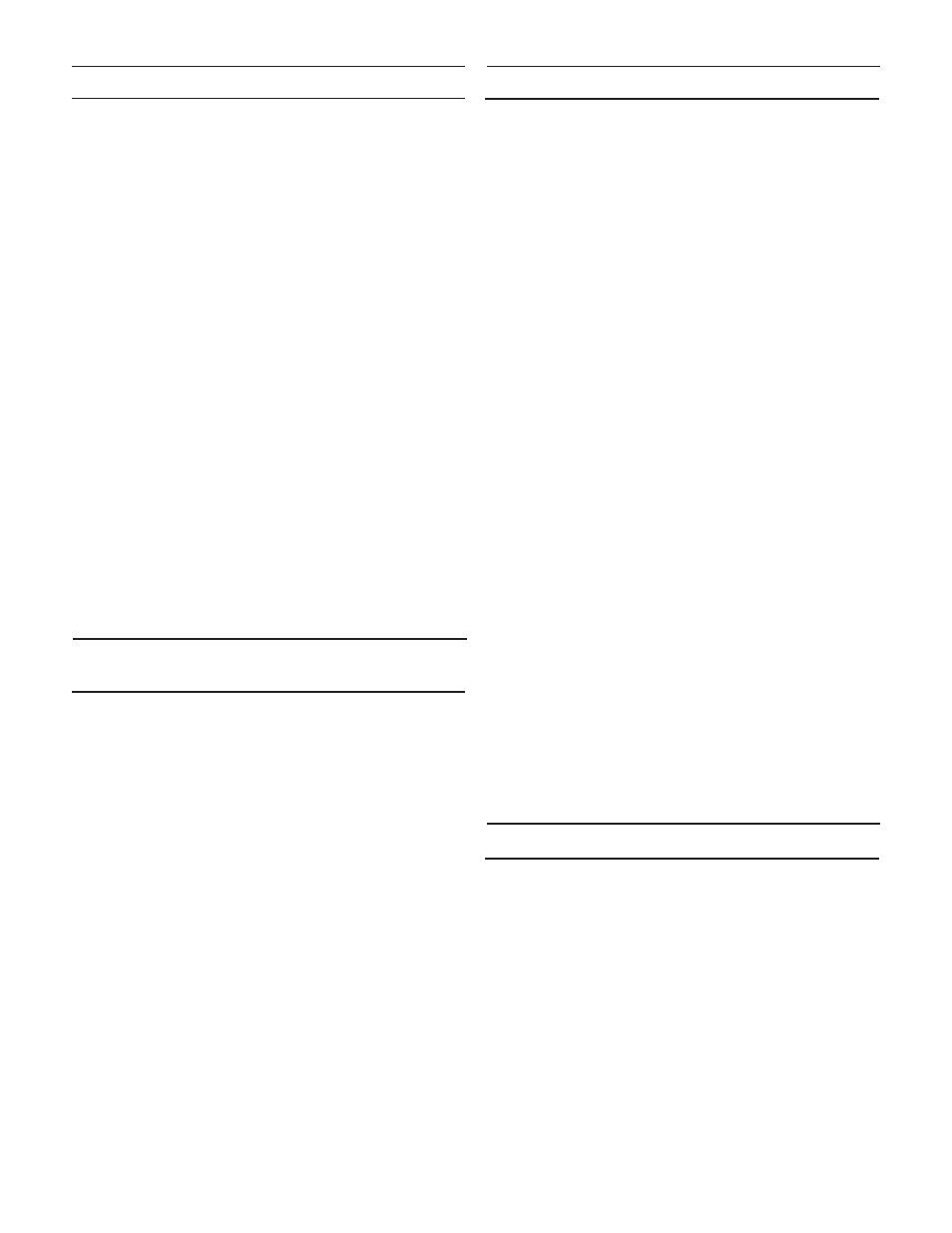
Reassembly of Actuator
After all parts have been thoroughly cleaned and in-
spected, reassemble the actuator:
Assemble actuator bolt (22), fastener seal (18), seal
1.
washer (17) (with counter bore towards actuator
bolt), diaphragm (16), diaphragm plate (15), spacer
(27) and thread into the actuator stem (11) and
tighten.
Set the diaphragm assembly down on a flat sur-
2.
face with the actuator stem facing up. Place small
amount of Parker O-Lube or comparable lubricant
on the actuator stem. Then place the inner and
outer springs (38 & 39) on the diaphragm plate,
nested over the stamped bosses, and one set in
the middle over the actuator stem (11).
Take the yoke/ lower case assembly and place
3.
over the springs, centering the actuator stem (11)
over the gland (12). Now take this entire assembly
firmly holding the diaphragm assembly and the
lower actuator case (9) together and flip it over
(making sure the springs do not move out of posi-
tion and are not hitting on any bolt heads (24A)
from the lower case).
Place the upper actuator case (23) on the dia-
4.
phragm, lining up the bolt holes.
Place the 2 longer bolts (24B) and nuts (25) 180°
5.
apart and tighten evenly to draw the upper case
(23) down onto the lower case (9). Install the re-
maining bolts and nuts and tighten evenly while
alternating across the actuator case.
35M Reverse Acting Actuator ATC
(Air to Close)
Assemble actuator bolt (22), spacer (27), dia-
1.
phragm plate (15), diaphragm (16), seal washer (17)
(with counter bore towards actuator stem), fastener
seal (18) and thread into the actuator stem and
tighten.
Place diaphragm assembly down into lower case/
2.
yoke assembly made in step 2, making sure to
guide the actuator stem thru the gland. Line up the
holes in the diaphragm (16) with the holes in the
lower diaphragm case (9).
Place the inner and outer springs (38 & 39) on
3.
the diaphragm plate, nested over the stamped
bosses, and one set in the middle over the actua-
tor bolt(22)
Place the upper actuator case (23) on the dia-
4.
phragm (16), lining up the bolt holes.
Place the 2 longer bolts (24B) and nuts (25) 180°
5.
apart and tighten evenly to draw the upper case
(23) down onto the lower case (9). Install the
remaining bolts (24A) and nuts (25) and tighten
evenly while alternating across the actuator case.
Trouble Shooting
If You Experience Erratic Control:
Oversizing can cause cycling or hunting (recalcu-
late the size required).
Undersizing can cause the control point to drop
off under peak loads (increase the trim size).
Inlet pressure to the valve maybe varying signifi-
cantly and the controller may not be following it
(adjust the controller).
Control loop may require equal percentage trim
if high rangabilities are being utilized. Steam traps
may need reconditioning.
Safety relief valves may be leaking.
Valve stroke may be out of adjustment or there
may be foreign matter in the valve preventing full
movement.
If You Experience Insufficient Flow:
Check shutoff valves to be sure they are fully open.
Inlet pressure to valve may be insufficient to pro-
vide the needed flow (check the inlet pressure with
a pressure gauge).
Strainers should be checked for clogging and
blown down if needed.
Steam traps may need reconditioning.
Dirt in the trim may prevent the valve from passing
its full capacity.
Diaphragm failure or insufficient air pressure to re-
verse acting (air-to-open) actuators would prevent
the valve from properly stroking open.
Incorrect actuator spring adjustment in reverse
acting actuators would prevent the valve properly
stroking open.
If You Experience Overpressure (outlet):
Dirt in the trim may prevent valve from shutting off.
Diaphragm failure, incorrect actuator spring adjust-
ment, or insufficient air pressure to direct acting
(air-to-close) actuators would prevent the valve
from properly stroking closed.
Ordering Spare Parts
Use only genuine Jordan Valve parts to keep your valve
in good working order. So that we can supply the parts,
which were designed for your valve, we must know ex-
actly which product you are using. The only guarantee to
getting the correct replacement parts is to provide your
Jordan Representative with the valve serial number. This
number is located on the valve identification tag. If the
serial number is not available, the parts needed for your
valve might be determined using the following informa-
tion: Model Number, Valve Body Size, Seat Material and
Cv Rating, Spring Range and Set Point, Trim Material, Part
Name - Number and Quantity.
NOTE: Any parts ordered without a valve serial number
that are found to be incorrect are subject to up to a mini-
mum 25% restock charge when returned.
-4-