Troubleshooting guide, Preventive maintenance, Recommended spare parts – Groth 3011L User Manual
Page 11: Table 6 – soft goods kits
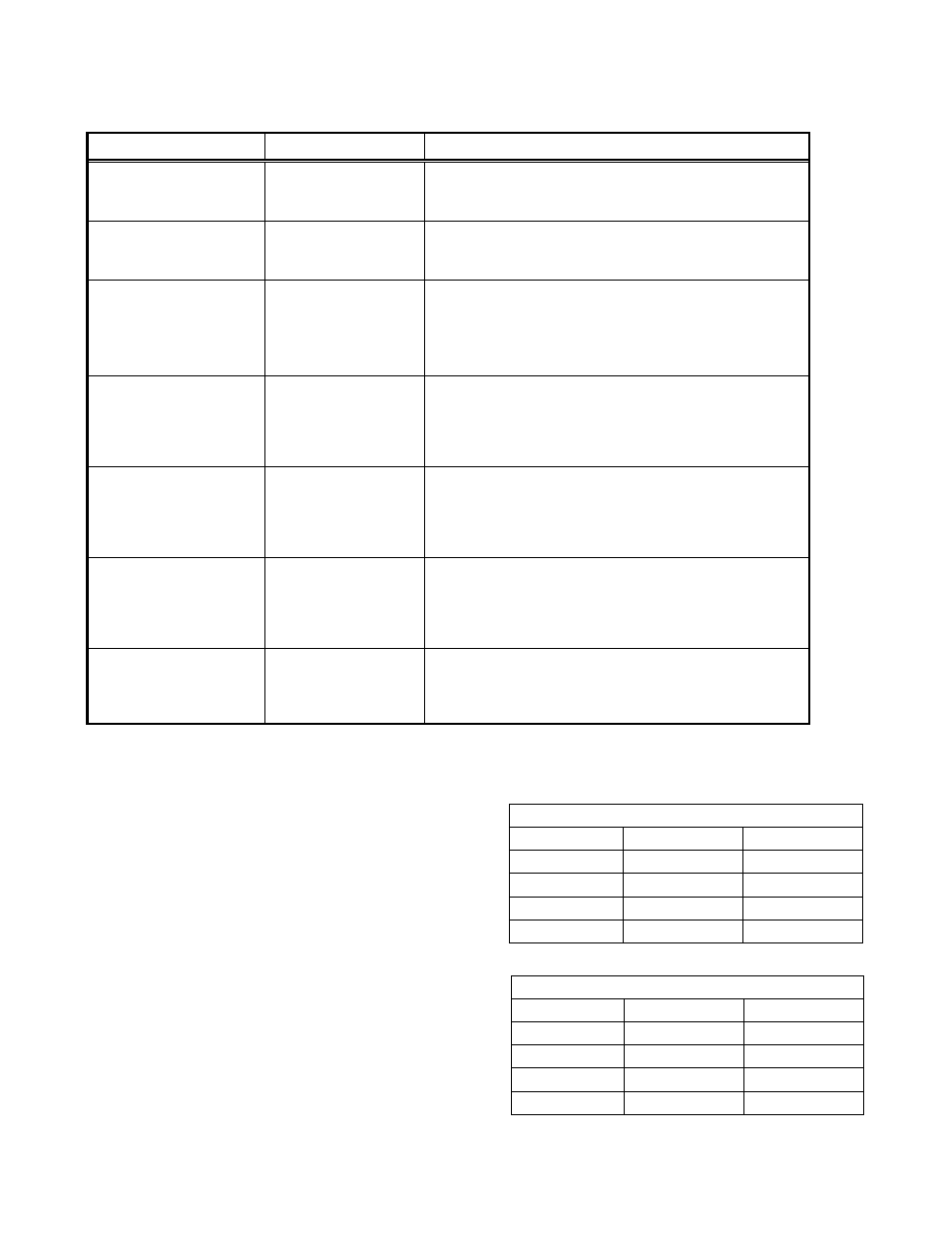
10
TROUBLESHOOTING GUIDE
PROBLEM
INSPECTION
SUGGESTED CORRECTIVE ACTION
Gas flowing at tank
pressure above
specified set point.
Flow indicator in
blanket gas line.
Damaged seat, O-Ring or diaphragm or pressure setting
too high. If original pressure setting has not been
disturbed, remove regulator and repair.
Gas not flowing at tank
pressure below
specified set point.
Flow indicator in
blanket gas line.
Damaged spring or pressure setting too low. If original
pressure setting has not been disturbed, remove
regulator and repair.
Gas leaking from upper
vent or bonnet
flange.
Soap bubble test and
joining surface or
emission
indication near the
regulator.
Damaged upper piston diaphragm. Remove regulator from
tank and replace diaphragm. Diaphragm installed
incorrectly. Reinforcement fabric must be opposite to
pressure (see page 12).
Blanket gas leaking from
lower body seal or
actuator housing
vent.
Soap bubble test at
joining surface or
emission
indication near the
regulator.
Damaged lower piston diaphragm. Remove regulator from
tank and replace diaphragm. Diaphragm installed
incorrectly. Reinforcement fabric must be opposite to
pressure (see page 12).
Process vapor leaking
from actuator
housing flange or
vent.
Soap bubble test at
joining surface or
emission
indication near the
regulator.
Damaged actuator diaphragm or loose housing bolts.
Tighten bolts or remove regulator from tank and
replace diaphragm.
Tank pressure above or
below specified
operating range
during pump out or
pump in.
Observe tank pressure
indicator during
pumping
operations.
Excess or insufficient blanket gas flow. Check flow orifice
orientation. Refer to Tables 4 & 5 for flow capacity
data. Check gas supply pressure. Remove and repair
regulator if other conditions are correct.
Tank pressure or vacuum
exceeds vent
settings during pump
out or pump in.
Observe tank pressure
indicator during
pumping
operations.
Pressure/vacuum relief vent not functioning or not sized
properly. Inspect and repair or replace as necessary.
PREVENTIVE MAINTENANCE
Periodically, while in service, examine the regulator for
leakage at bolted connections, adjusting screws, etc. Test
for blanket gas or process vapor emissions from vent caps.
RECOMMENDED SPARE PARTS
The following spare parts should be stocked for maintenance
purposes:
Spring [34]; See Table 3 for the correct part number.
Vent [24]; part number 10064003
Soft Goods Kit; See Table 6 for the correct part number.
When ordering spare parts, include model and serial number
of regulator, pressure setting, and required material for soft
goods.
TABLE 6 – SOFT GOODS KITS
1/2" BGR
Elastomer 3011L
3011H
Buna-N KS3011L05B
KS3011H05B
FFKM KS3011L05C
KS3011H05C
EPDM KS3011L05E
KS3011H05E
FKM KS3011L05V
KS3011H05V
1" BGR
Elastomer 3011L
3011H
Buna-N KS3011L01B
KS3011H01B
FFKM KS3011L01C
KS3011H01C
EPDM KS3011L01E
KS3011H01E
FKM KS3011L01V
KS3011H01V