Insinger GalleyMaster Series User Manual
Page 25
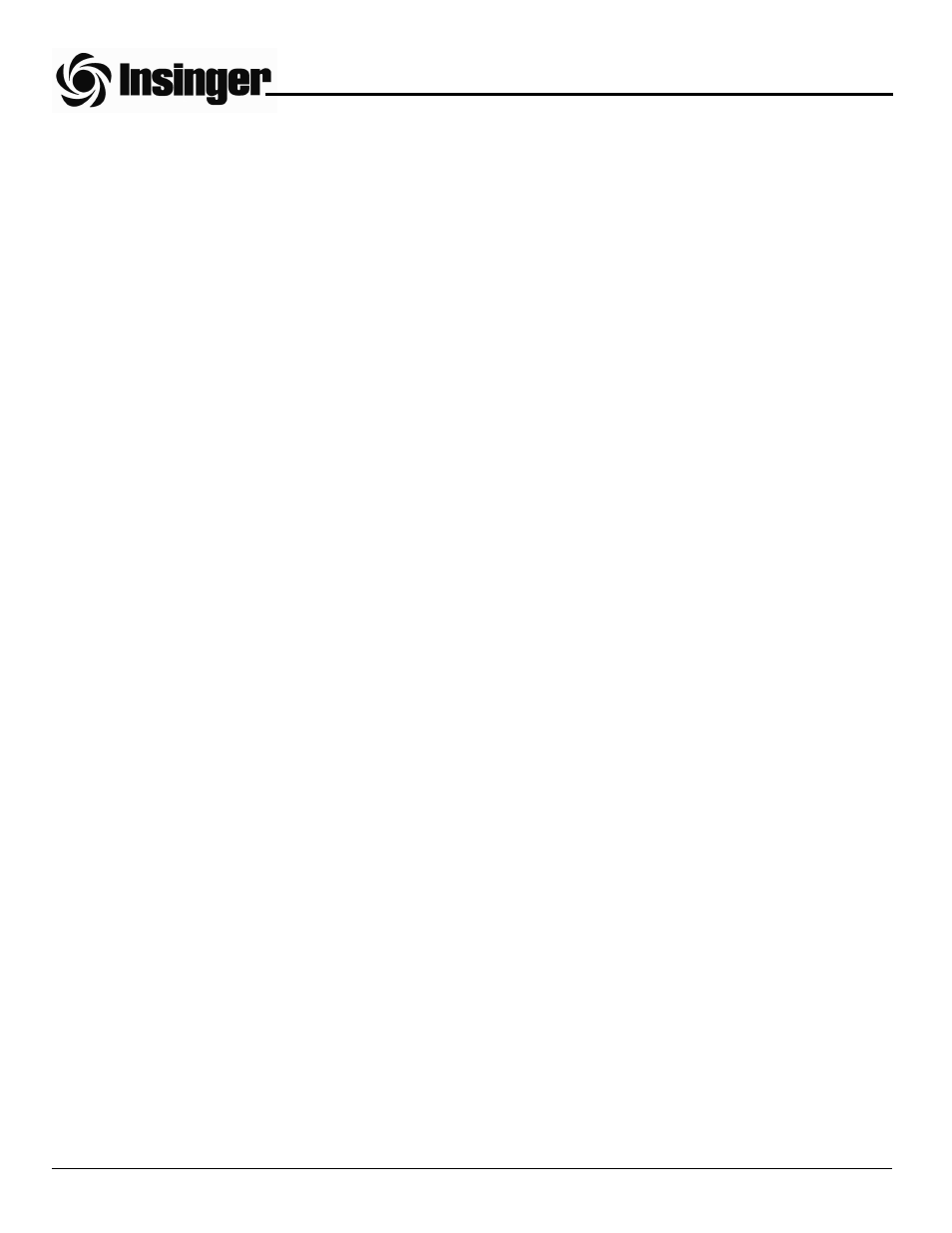
Wash and rinse thermometers. See Figure 6-3.
1. Remove the thermometer guard from the outside of
the tank.
2. Using a wrench on the hex of the thermometer
(behind the dial), unscrew the thermometer from the
thermometer well. Do not unscrew by turning the dial
case.
3. Install a new thermometer. Use Teflon tape on the
threads, so the thermometer is "snug" with the 100°
mark at 12 o'clock. Use a wrench on the hex but do not
overtighten.
4. Replace the thermometer guard.
Final hot rinse thermometer. See Figure 6-4.
Using a wrench on the hex boss of the rinse thermome-
ter stem, unscrew the thermometer from the tee in the
final rinse line, and replace with a new unit.
Overload relay settings and functions. See Figure 6-5.
Overload current setting. Lift the plastic cover. With a
small screwdriver, align the set point on the overload
setting dial with the value for the motor nameplate full
load current for 440 volts. The nominal full load current
for 440 volt operation of a typical 3 phase motor is:
1 hp. (pump)
2.2 amps
1/3 hp. (loader)
0.8 amps
1/4 hp. (unloader pushout drive)
0.7 amps
1/15 hp. (unloader roller & conveyor drive) 0.16 amps
Auto reset selection. The overload relay is factory in-
stalled in the auto reset configuration. A blue shutter
appears in the reset selector window. Always use this
configuration. If set to the manual reset function (which
may be the case with a replacement part), a white plas-
tic cover with an "H" covers the reset selector window.
To change to auto reset, lift the plastic cover. Use a
small screwdriver to pry off and discard the "H" cover.
Slide the blue shutter downward until a faint "click" is
heard.
Reset test. To test the overload trip function, press the
red Stop button. The NC auxiliary contact (only) will
open as long as the Stop button is pressed in. This con-
tact is wired in series with other overload relay NC auxil-
iary contacts and, when opened, will stop all motors.
Adjust tank temperature.
The wash tank temperature should be 150° to 155° F.
The rinse tank temperature should be 160° to 165° F.
Temperature adjustment. Tank temperature is sensed
by a thermistor on the tank wall and regulated by a tem-
perature control board in the electrical control enclosure.
See Figure 6-6. Locate the tan adjustment pot with slot
on the wash or rinse tank temperature control board.
Rotate in small increments (CW to increase, CCW to
decrease temperature) and allow tank temperature to
stabilize between adjustments.
Control board replacement. To replace the tank heat
temperature control board or thermistor, disconnect and
tag all wires, and then remove the board or thermistor.
Adjust rinse booster temperature.
The booster water outlet temperature should be 190° to
195° F.
Steam heated booster. The temperature controller is on
the front of the booster. Unscrew the round cover. See
Figure 6-7. The water outlet temperature control switch
is on the left, marked "Temp Set 190° F." Use a hex key
to rotate the pointer and change the setting. Higher
scale settings correspond to higher outlet temperatures.
While the rinse is operating, turn the pointer in 1/2 scale
increments and observe the rinse temperature over sev-
eral rinse cycles.
The switch on the right is the low water temperature in-
terlock switch, factory set at 180° F.
To remove this thermostat, first close the manual hot
water valve. Disconnect and tag all wires. Remove the
electrical conduit from the thermostat housing. Unscrew
the entire thermostat assembly from the pipe tee on the
booster.
Electrically heated booster.
The thermostat is located inside the lower front of the
booster. Remove the access plate marked "Remove for
access to thermostats and high limit switch". See Figure
6-8. Rotate the slotted screw "G" in small increments
CCW to lower temperature. Rotate nut "F" CCW, while
holding "G" against high stop, to raise temperature. Al-
low tank temperature to stabilize between adjustments.
Note that 1/6 turn is approximately 12° F. Observe the
rinse temperature over several rinse cycles.
PART 4 MAINTENANCE & REPAIR PROCEDURES