NIStune Type 4 User Manual
Page 7
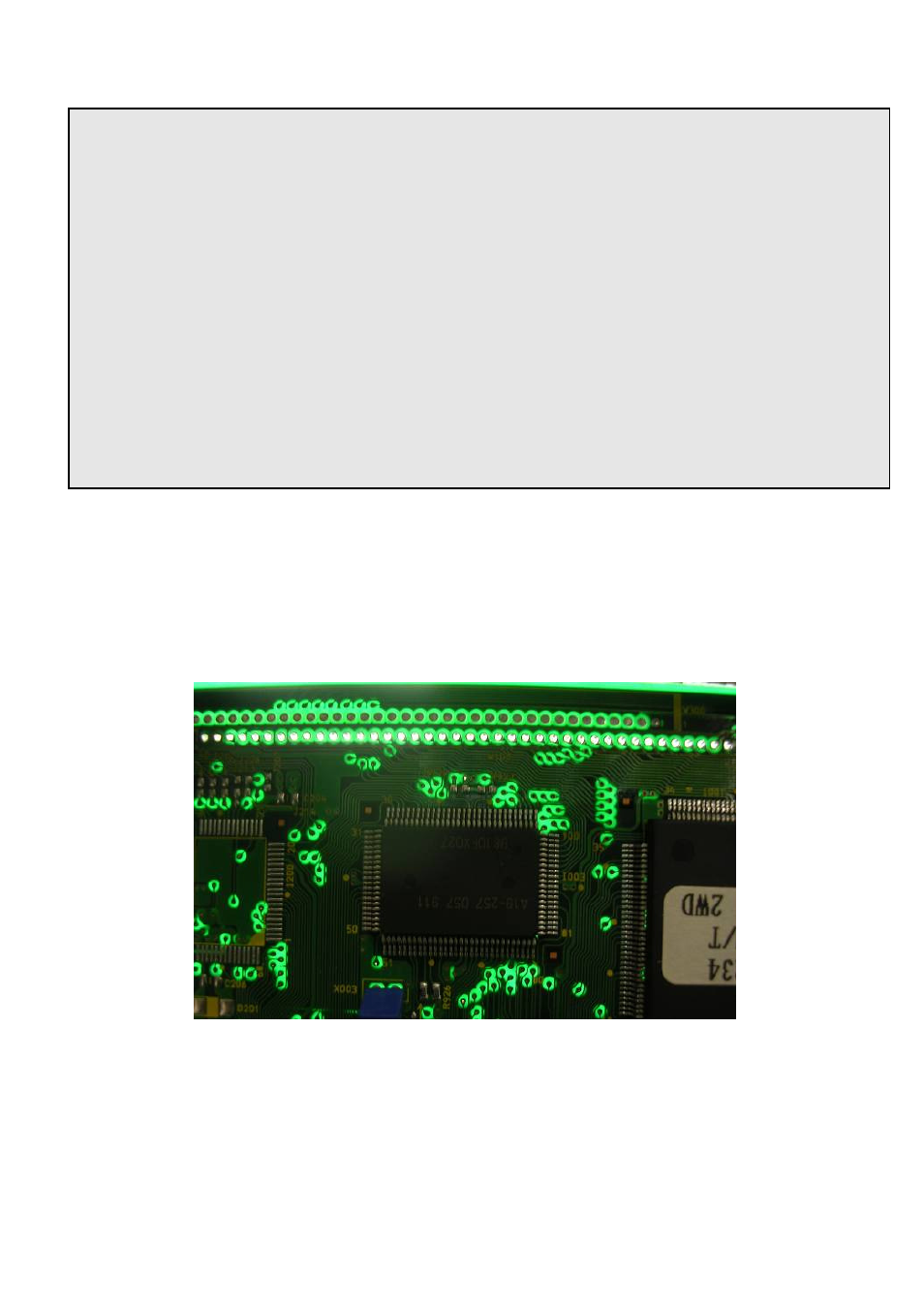
Type 4 Hardware Installation Manual
Page 6 of 21
Tips: The best way to de-solder the pads is to run a line of flux down the row of pads you intend to work on. This
will provide a heat-bridge between the de-soldering gun and the solder in the pads. Do not push on the pads
otherwise you will damage them – try to hold the iron so it only just touches the pad.
Note that these ECUs use multi layered boards. The middle layer usually consists of ground and VCC copper planes.
These absorb a lot of heat and make the de-soldering process quite difficult, due the amount of temperature they soak
up from the gun. Heating the area with a hot air gun will help. Apply heat mainly from rear of board to avoid
damaging main components which are on the top side. Don’t overheat the board. You should still be able to *just*
touch the board.
Ground planes will connect to pads on these connectors, where one pad (pin 1) is VCC plane and two pads (19/20 on
Adaptor A boards and pin 39/40 on Adaptor B/C boards) are ground planes. A good quality iron will remove the
solder from these pads without a problem, although you may need to increase the time on the pad from the usual 0.5
– 1 second to 1 – 3 seconds.
Another technique is to stand the ECU vertically and use the de-soldering iron from one side of the board and a
soldering iron from the other side. This heats the solder from both sides of the pad. This is a particularly effective
method but requires considerable skill and is ideally done with help from an assistant.
Warning: Pads on these ECUs are very delicate. Don’t attempt this unless you have the right
equipment. It’s quite easy to damage the board. Don’t overheat the pads (about a second per pad is
a safe maximum) or damage can easily result. If in doubt get somebody with the right equipment to
do it for you.
Check that holes are clear
Hold the ECU up to the light and check that all the holes are clear. If any holes still have solder in them
do not try to clear them out using a drill bit! The boards are multi-layer and it is quite likely that an
internal connection will be damaged.
If some holes are not clear then reapply solder to both sides of the hole – this helps create a more
effective “heat bridge” between the iron and the solder. Then re-attempt de-soldering. It’s usually only
pads that connect to power or ground that cause problems.
It is very important the holes are completely clear, otherwise it will make the next step impossible when
attempting to insert the strip connectors.