Aec 200-4d specifications, Warning, Preweld check list – Profax AEC 200-4D User Manual
Page 5: Shutting down, Maintenance
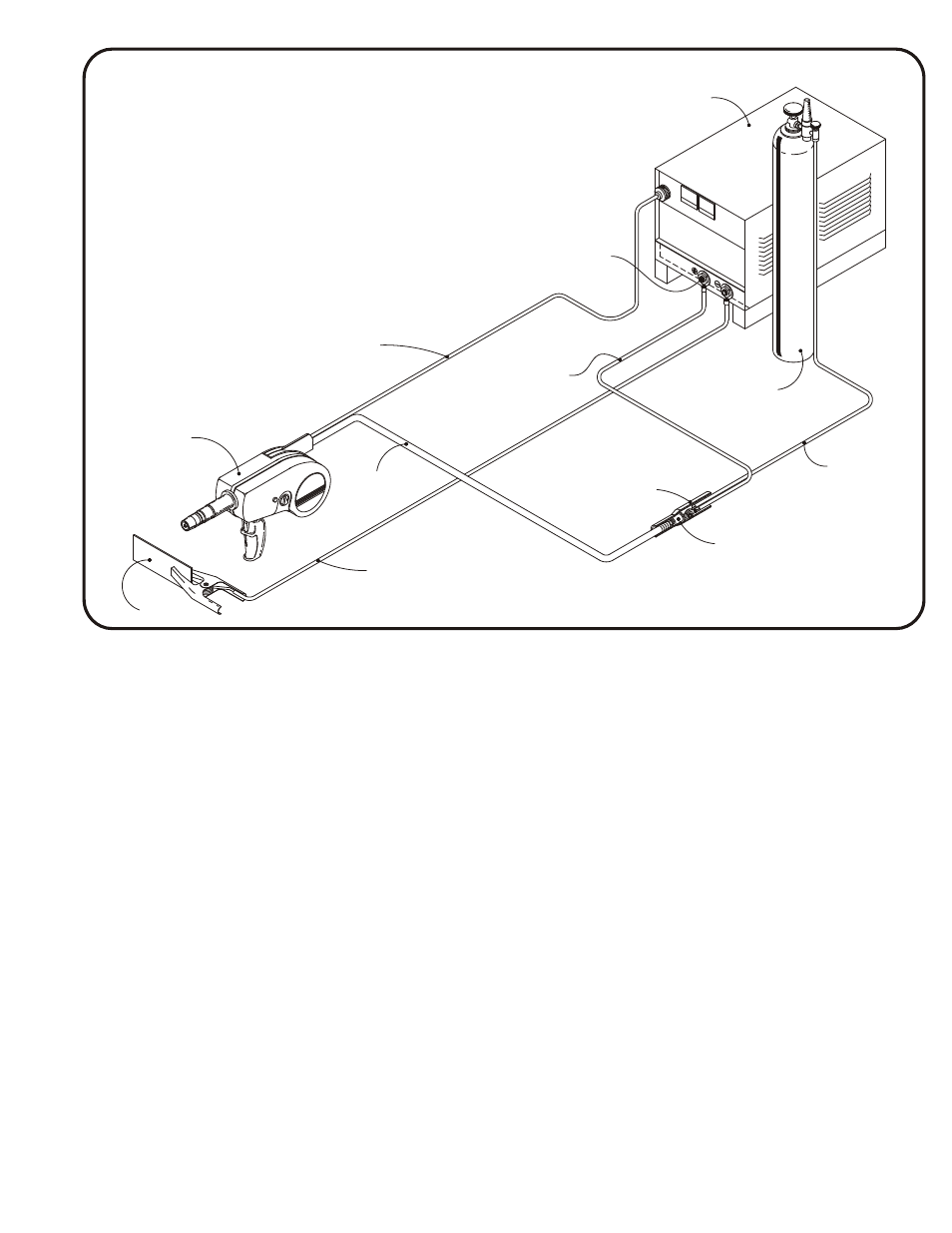
2
3
AEC 200-4D SPECIFICATIONS
Input Power
Weld Output Rating
Wire Capacity
Wire Speed Range
Dimensions
Weight
Argon or Helium
Gun & Cables
250 Amps
.030 - 1/16”
20 ipm
Height 8.25"
Net
24VAC
50% Duty Cycle
Aluminum
to
Width 3"
26.8 lbs.
200 Amps
or
800 ipm
Length 15"
Ship
100% Duty Cycle
.023 - .045
29.8 lbs.
Hard Wire
The AEC 200-4D Direct Connect Spoolgun gives the improved SOLID STATE motor control performance to
®
®
the
Classic AEC 200 Spoolgun design. This system can be direct connected to any Comparc , Miller ,
®
Thermal Arc , or “PROFAX” CONSTANT VOLTAGE welding power source of adequate size and with 24VAC
auxiliary power available.
DIRECT CONNECT SPOOL GUN SYSTEMS
®
AEC 200-4DM
Direct Connect Spool Gun for Miller Constant Voltage power sources
with the 14 pin wire feeder receptacle.
®
AEC 200-4DMX
Direct Connect Spool Gun for the Millermatic 250X.
AEC 200-4DP
Direct Connect Spool Gun for “PROFAX” power sources.
MODEL NO.
DESCRIPTION
INSTALLATION (For help see fig. 1)
Figure 1
Connect the AEC 200-4D Direct Connect Spool Gun as follows:
1. Weld cable to the POSITIVE (+) terminal of the welding power source.
2. Control cable to the remote receptacle on the front of the welding power source.
3. Gas hose to the flowmeter/regulator at the gas supply.
DISCONNECT ALL ELECTRICAL POWER TO
THE WELDING POWER SOURCE BEFORE
INSTALLING THIS EQUIPMENT
WARNING!
PREWELD CHECK LIST
1. Make sure the AEC 200-4D Spool Gun is set up for wire size selected by having the proper liner, contact tube and nozzle.
2. Weld cable and hose is connected and tight. Control cable connection is fully inserted with the collar screwed on properly.
3. Mig wire is installed in a manner to allow the wire to feed from the top of the spool into the wire drive.
4. Proper shielding gas has been selected and the gas cylinder valve is on and backseated. Flowmeter properly set and hose line purged.
5. Power source on and correct voltage set.
6. Wire speed adjustment on Spool Gun is properly set.
7. Mig wire is through tip and extending just past end of nozzle.
NOTE: It is recommended to perform trial welds on scrap metal similar to what is going to be welded for adjusting proper wire speed, amps
and voltage settings. This will also familiarize you with the spool gun’s operating characteristics.
SHUTTING DOWN
After your welding job is complete or work is stopped for any appreciable amount of time proceed as follows:
1. Turn power source off.
2. Turn shielding gas off at the cylinder valve.
3. Make sure cover is secured onto spool gun.
MAINTENANCE
NOTE: Before performing any maintenance on this spool gun, BE SURE all sources of power have been TURNED OFF.
Check the following on a daily basis:
1. Inspect cables and hoses for frayed wiring or cracked insulation. Damaged wires and cable are hazardous and must be replaced.
2. Clean any spatter, grease or grime from the interior and/or exterior of the spool gun to prevent short circuits.
3. Check all mounting screws for tightness.
4. Keep cover on at all times to minimize dirt and contaminants from entering spool gun.
CONSTANT VOLTAGE POWER SOURCE WITH THE AEC 200-4D SPOOL GUN
WORK
MODEL
AEC 200-4D
SPOOL GUN
MULTI CONDUCTOR
CABLE TO REMOTE
RECEPTACLE ON
POWER SOURCE
POSITIVE OUTPUT
TERMINAL
WELDING CABLE TO POSITIVE
OUTPUT TERMINAL ON
POWER SOURCE
CABLE
BOOT
HOSE TO GAS
SUPPLY
GAS CYL.
POWER
SOURCE
CONNECTION
BLOCK
WELDING CABLE FROM
NEGATIVE OUTPUT TERMINAL
ON POWER SOURCE
GAS & WELDING
CABLE