Flowserve MN User Manual
Page 37
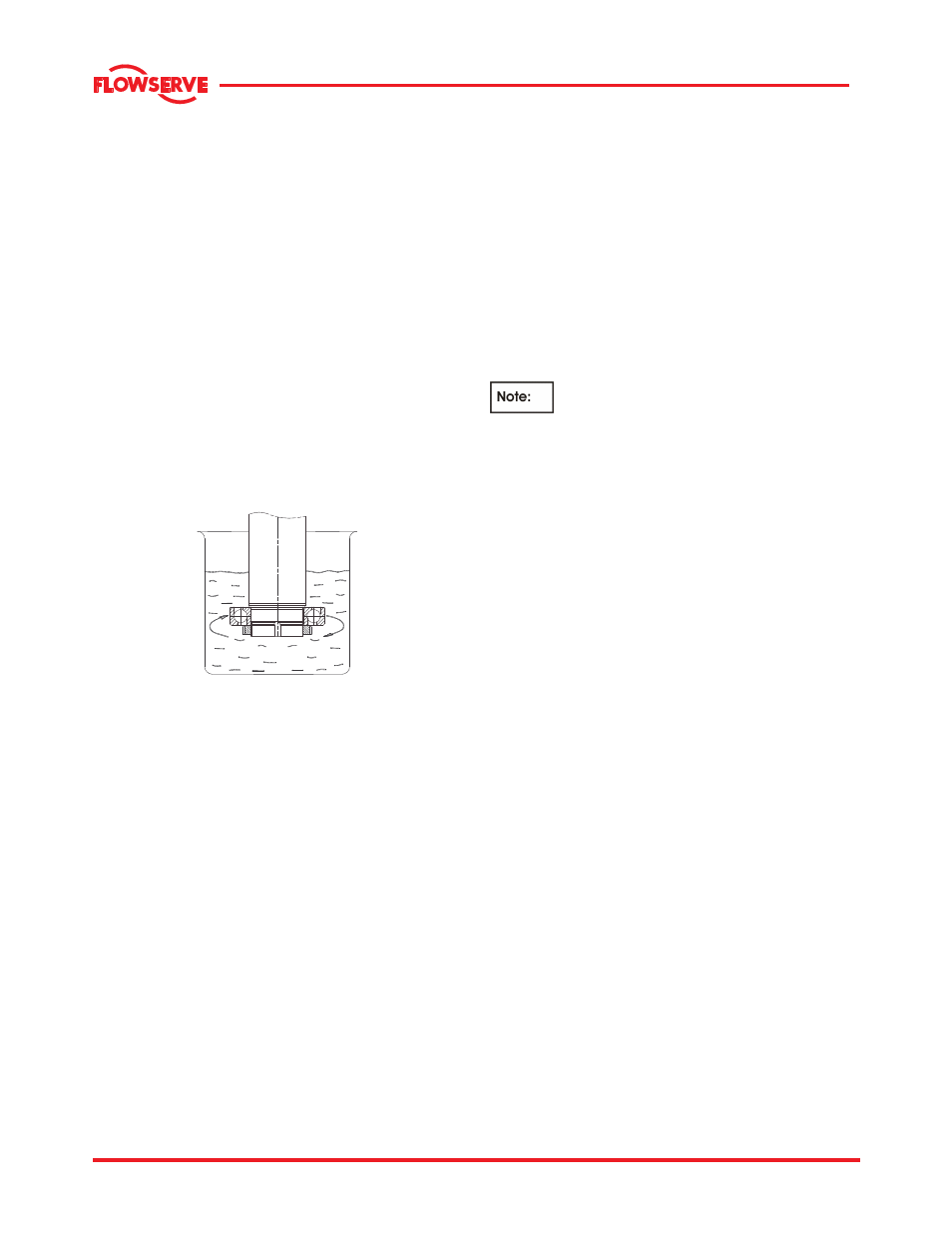
MN USER INSTRUCTIONS ENGLISH 71569189 11/04
Page 37 of 49
®
6.1.10.4 To clean the bearings
a) Wipe off as much grease as possible with a clean
lint-free cloth.
b) Brush bearings with hot oil or non-toxic solvent
80 to 95
o
C (180 to 200
o
F ) while gently spinning
the outer bearing ring.
c) Spin each roller to ensure that it is clean.
6.1.10.5 To remove badly oxidized grease
a) Support the rotor in a vertical position and
immerse the bearing in hot oil 80 to 90 °C (175 to
195 °F) or a mixture of alcohol and light mineral
solvent.
b) Dry and re-flush the bearing with clean light oil.
c) It is important not to under or over grease the
bearings as this will lead to over heating and
premature failure. It is recommended that the
bearings be filled with grease using a suitable
spatula. In addition the housings should be no
more than half filled.
6.1.11 Mechanical seals
No adjustment is possible. When leakage reaches
an unacceptable level the seal will need replacement.
6.1.12 Gland packing
The stuffing box split gland can be completely
removed for re-packing or to enable the addition of
extra rings of packing.
The stuffing box is normally supplied with a lantern
ring to enable a clean or pressurized flush to the
center of the packing. If not required, this can be
replaced by an extra 2 rings of packing.
There must always be a small leakage, normally a
minimum of 30~60 drops per minute is required
depending upon the sleeve diameter.
6.2 Spare parts
6.2.1 Ordering of spares
Flowserve keep records of all pumps that have been
supplied. When ordering spares the following
information should be quoted:
a) Pump serial number.
b) Pump size.
c) Part name –
Refer to section 8.
d) Part number –
Refer to Section 8.
e) Number of parts required-Quantity.
The pump size and serial number are shown on the
pump nameplate.
To ensure continued satisfactory operation,
replacement parts to the original design specification
should be obtained from Flowserve. Any change to
the original design specification (modification or use
of a non-standard part) will invalidate the pump’s
safety certification.
6.2.2 Service parts
The severity of the condition of service, the extent to
which repairs can be carried out in the field, and the
number of units installed will determine, to a great
extent, the minimum number of service parts that
should be carried in stock at the installation site. It is
suggested, as insurance against delays, that service
parts be purchased at the time the pump order is
placed or as soon after receiving the pump as
possible.
A suggested spare parts list (priced if desired) can be
furnished upon request.
6.2.3 Returning parts
All material returned to the factory must have a
returned material (RM) tag attached. Consult the
nearest Flowserve sales office or OEM factory for
shipping instructions and "RM" tags. Unnecessary
delays are avoided when parts or equipment are
returned to the proper factory using the correct
procedure.
a) When contacting the sales office or factory for
return authorization, list the material to be
returned and the reasons for returning it.
b) On receipt of the "RM" tags, be sure to check the
part name, the part number, the quantity of parts
involved, and the serial number of the equipment.
c)
The "RM" tag must accompany the material
shipped. Enclose it in the shipping container or
attach it to the part being returned
.