Machine integration, Machine integration – contents 4 – HEIDENHAIN TNC 335 Technical Manual User Manual
Page 98
Advertising
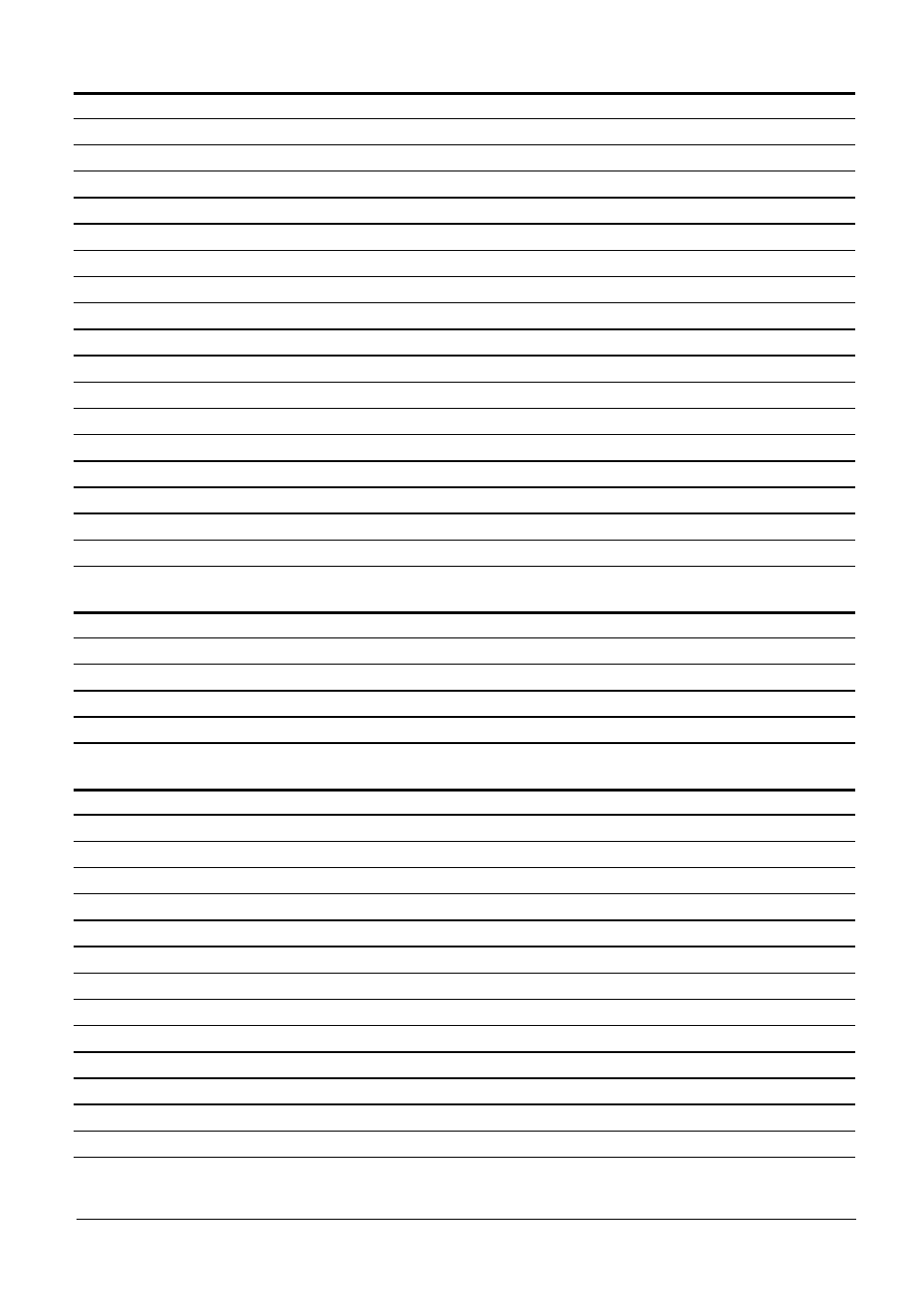
8/95
TNC 360
1 Machine Axes
4-1
Machine Integration – Contents
4
Compensation for reversal errors in circular motion
Linear axis-error compensation
Nonlinear axis error compensation
Passing over the reference marks
2.1.1 Measuring systems with distance-coded reference marks
2.1.2 Measuring systems with one reference mark
2.1.3 Linear measurement via rotary encoder
Servo positioning of the NC-axes
The position control loop of an NC-machine
Servo positioning in TNC controls
3.2.2 Control with feed forward
3.3.1 Offset adjustment by code number
3.3.2 Automatic cyclical offset adjustment
3.3.3 Offset adjustment with integral factor
3.4.2 Constant feed rate in corners
3.4.3 Constant feed rate in corners with M90
Advertising