HEIDENHAIN iTNC 530 (340 49x-04) ISO programming User Manual
Page 338
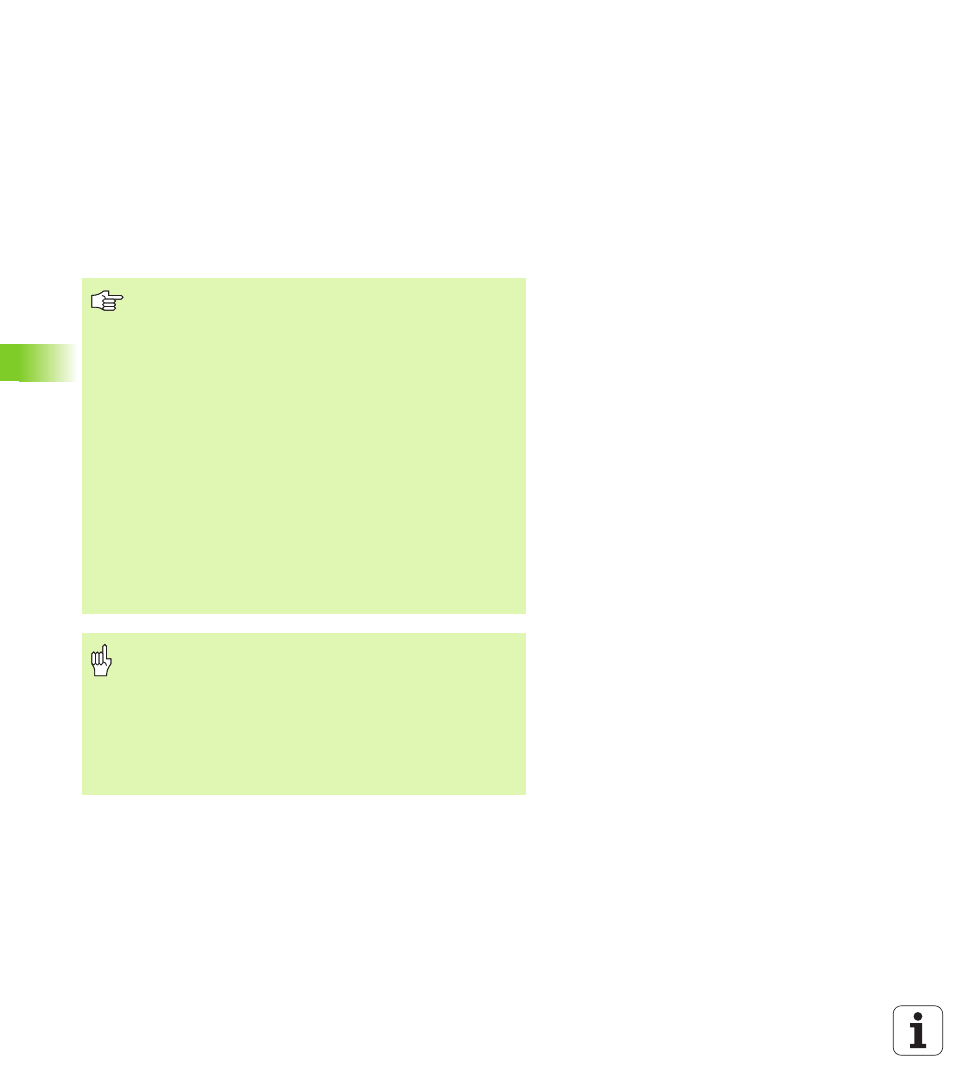
338
8 Programming: Cycles
8.3 Cy
cles f
o
r Dr
illing, T
a
pping and Thr
ead Milling
Thread milling
8
The TNC moves the tool at the programmed feed rate for pre-
positioning to the starting plane for the thread. The starting plane
is determined from the thread pitch and the type of milling (climb
or up-cut).
9
Then the tool moves tangentially on a helical path to the thread
diameter and mills the thread with a 360° helical motion.
10 After this, the tool departs the contour tangentially and returns to
the starting point in the working plane.
11 At the end of the cycle, the TNC retracts the tool at rapid traverse
to the set-up clearance, or—if programmed—to the 2nd set-up
clearance.
Before programming, note the following
Program a positioning block for the starting point (hole
center) in the working plane with radius compensation
G40.
The algebraic sign of the cycle parameters depth of thread,
countersinking depth or sinking depth at front determines
the working direction. The working direction is defined in
the following sequence:
1st: Depth of thread
2nd: Countersinking depth
3rd: Depth at front
If you program a depth parameter to be 0, the TNC does
not execute that step.
If you want to countersink with the front of the tool, define
the countersinking depth as 0.
Program the thread depth as a value smaller than the
countersinking depth by at least one-third the thread pitch.
Enter in MP7441 bit 2 whether the TNC should output an
error message (bit 2=1) or not (bit 2=0) if a positive depth
is entered.
Danger of collision!
Keep in mind that the TNC reverses the calculation for pre-
positioning when a positive depth is entered. This
means that the tool moves at rapid traverse in the tool axis
at safety clearance below the workpiece surface!