Rotation (cycle g122), 6 sl c y cles – HEIDENHAIN iTNC 530 (340 49x-04) ISO programming User Manual
Page 405
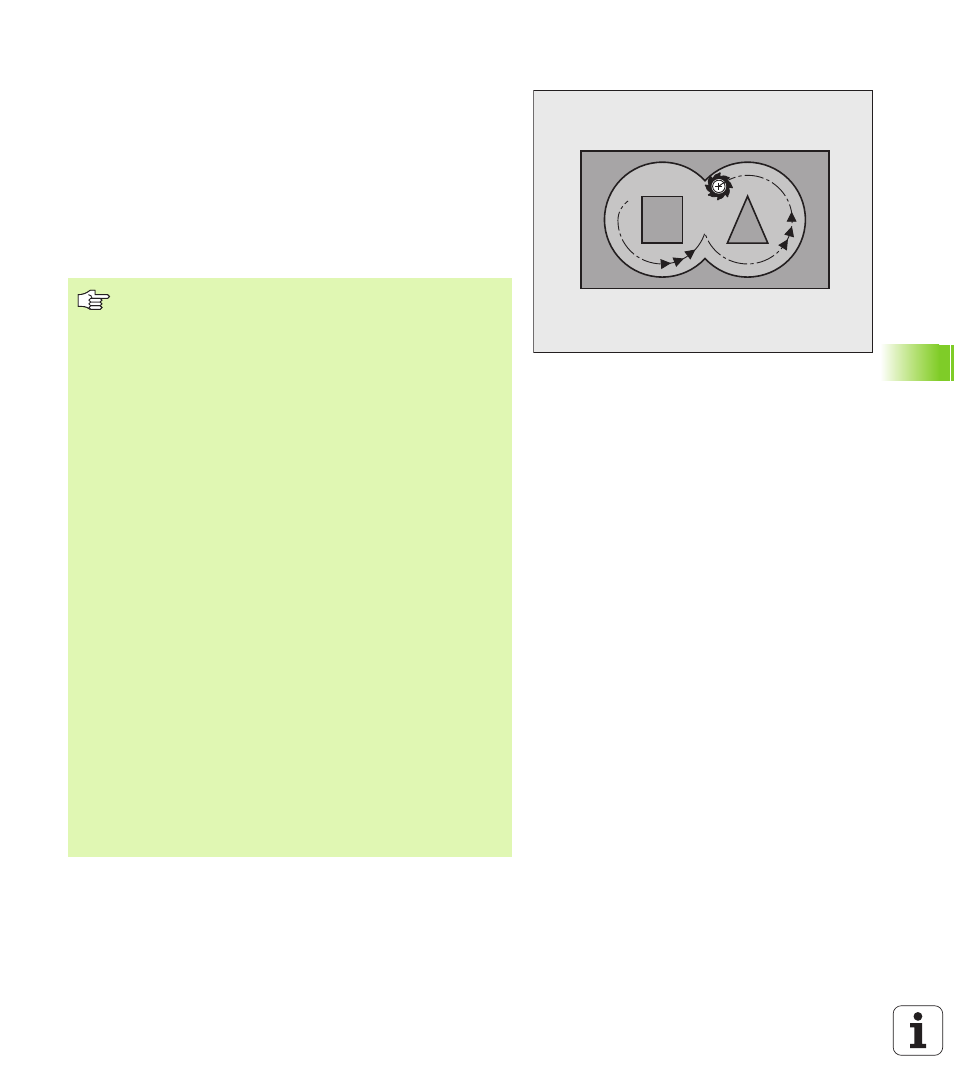
HEIDENHAIN iTNC 530
405
8.6 SL c
y
cles
ROTATION (Cycle G122)
1
The TNC positions the tool over the cutter infeed point, taking the
allowance for side into account.
2
In the first plunging depth, the tool mills the contour from the
inside outward at the milling feed rate Q12.
3
The island contours (here: C/D) are cleared out with an approach
toward the pocket contour (here: A/B).
4
In the next step the TNC moves the tool to the next plunging depth
and repeats the roughing procedure until the program depth is
reached.
5
Finally the TNC retracts the tool to the clearance height.
Before programming, note the following
This cycle requires a center-cut end mill (DIN 844) or pilot
drilling with Cycle G121.
You define the plunging behavior of Cycle 22 with
parameter Q19 and with the tool table in the ANGLE and
LCUTS columns:
If Q19=0 is defined, the TNC always plunges
perpendicularly, even if a plunge angle (ANGLE) is
defined for the active tool.
If you define the ANGLE=90°, the TNC plunges
perpendicularly. The reciprocation feed rate Q19 is used
as plunging feed rate.
If the reciprocation feed rate Q19 is defined in Cycle 22
and ANGLE is defined between 0.1 and 89.999 in the
tool table, the TNC plunges helically at the defined
ANGLE.
If the reciprocation feed is defined in Cycle 22 and no
ANGLE is in the tool table, the TNC displays an error
message.
If geometrical conditions do not allow helical plunging
(slot geometry), the TNC tries a reciprocating plunge.
The reciprocation length is calculated from LCUTS and
ANGLE (reciprocation length = LCUTS / tan ANGLE)
If you clear out an acute inside corner and use an overlap
factor greater than 1, some material might be left over.
Check especially the innermost path in the test run graphic
and, if necessary, change the overlap factor slightly. This
allows another distribution of cuts, which often provides
the desired results.
During fine roughing the TNC does not take a defined wear
value DR of the coarse roughing tool into account.