HEIDENHAIN TNC 306 Technical Manual User Manual
Page 498
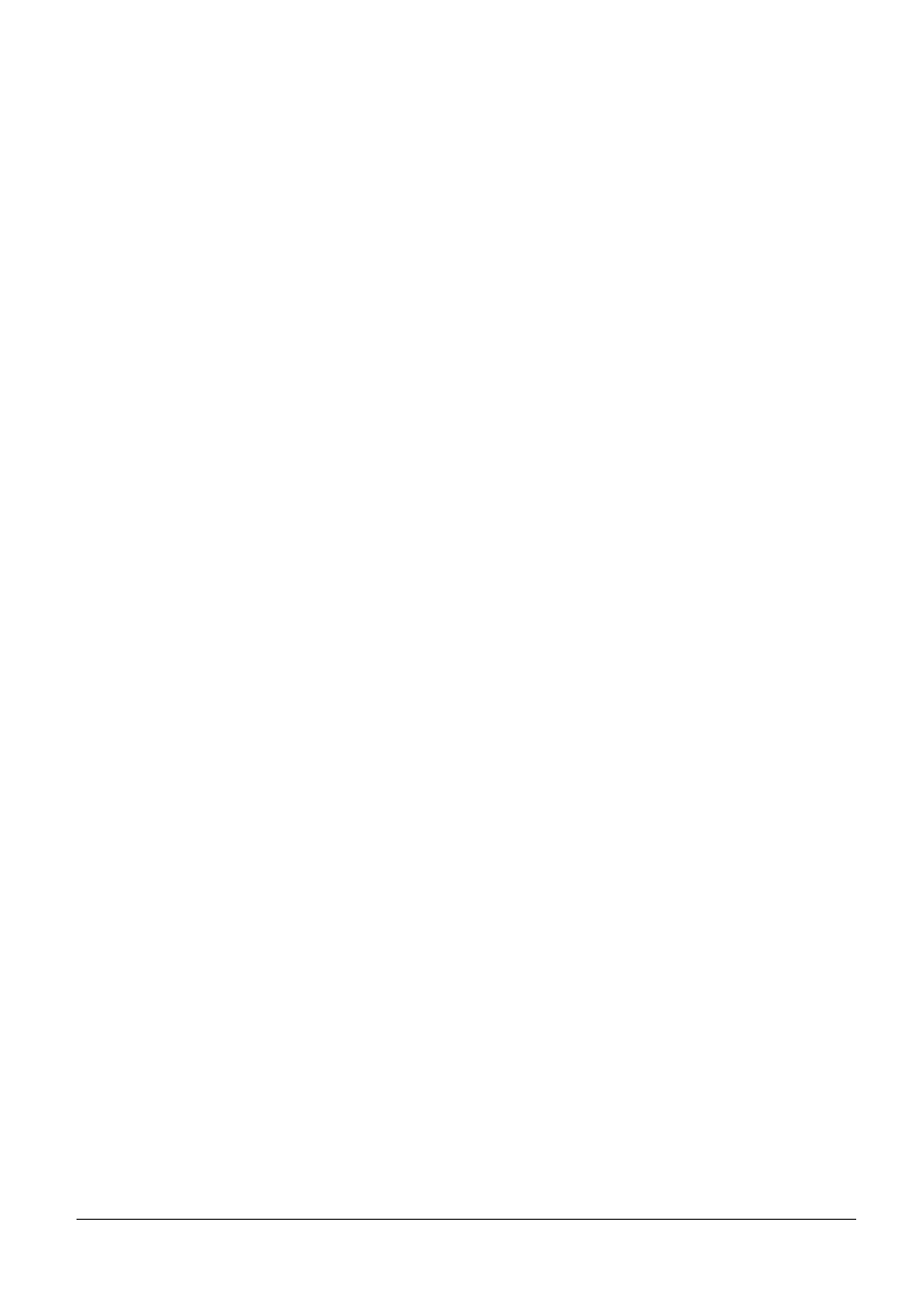
3/98
TNC406/TNC 306
1-3
• Servo Sensitivity SV is no longer read directly out of the corresponding byte of the erosion table,
but rather from the new byte B763. During control with a table, SV is automatically transferred to
B763. During control without a table (MP2199=0), the value of the corresponding SV-Q
parameter in the PLC program can be transferred to B763, and SV can therefore be changed
during erosion.
• The step-output function was modified so that the duration of output can be determined by
pressing the key. This also makes it possible to move across larger distances with constant
voltage.
• Markers 2688 and following (switching off monitoring functions in the control loop) was removed
to ensure safety.
• New machine parameter MP7651
With the new MP 7651 you can select whether the short circuit monitoring during manual
handwheel traversing is switched on or off.
Input:
0 = Switch short-circuit monitoring on
1 = Switch short-circuit monitoring off
• New Cycle 4 SPARK OUT TIME
The new Cycle 4 enables you to program the sparking out time during erosion in the range of
1...9999 seconds. This value remains effective until another Cycle 4 is run or the part program is
reselected. After reset or reselection the value from MP2110 becomes effective.
• Comment blocks are now also saved if they begin with a semicolon ”;” are now also saved. The
binary format of an NC block limits the string length of these comment blocks to 22 characters.
As before, comment blocks that begin with an asterisk ”*” are not saved.
A comment block is editable only if it begins with a semicolon. A comment can be
inserted only between the NC blocks. It is not possible to insert a comment at the end of an NC
block.
• Change in MP2081
The input range for MP2050 was expanded from 0..2 mm to 0..20 mm.
• New Cycle 19 WORKING PLANE for tilting the working plane
Now you can program up to three tilt angles for the axes A, B and C. The tilt angles are shown in
a special status window. The control uses the entered angle to calculate movement in axes X, Y
and Z. Positioning commands are executed in the tilted plane if Cycle 19 has been run and at the
same time an OEM cycle or the disk cycle is being run. Positioning commands outside an OEM
cycle and PLC positioning commands are always executed in an untilted plane.
The tilting point is the disk origin for Cycle 17 Disk, or the starting point of an OEM cycle
(30...99). The OEM cycle can be composed of any linear blocks and disks. Circles are not
possible in a tilted OEM cycle, which is indicated by the error message CIRCLE TILTING NOT
POSSIBLE.