7 general precautions for wiring – Yaskawa Σ-V Series AC Servo Drives Rotational Motor MECHATROLINK-III User Manual
Page 44
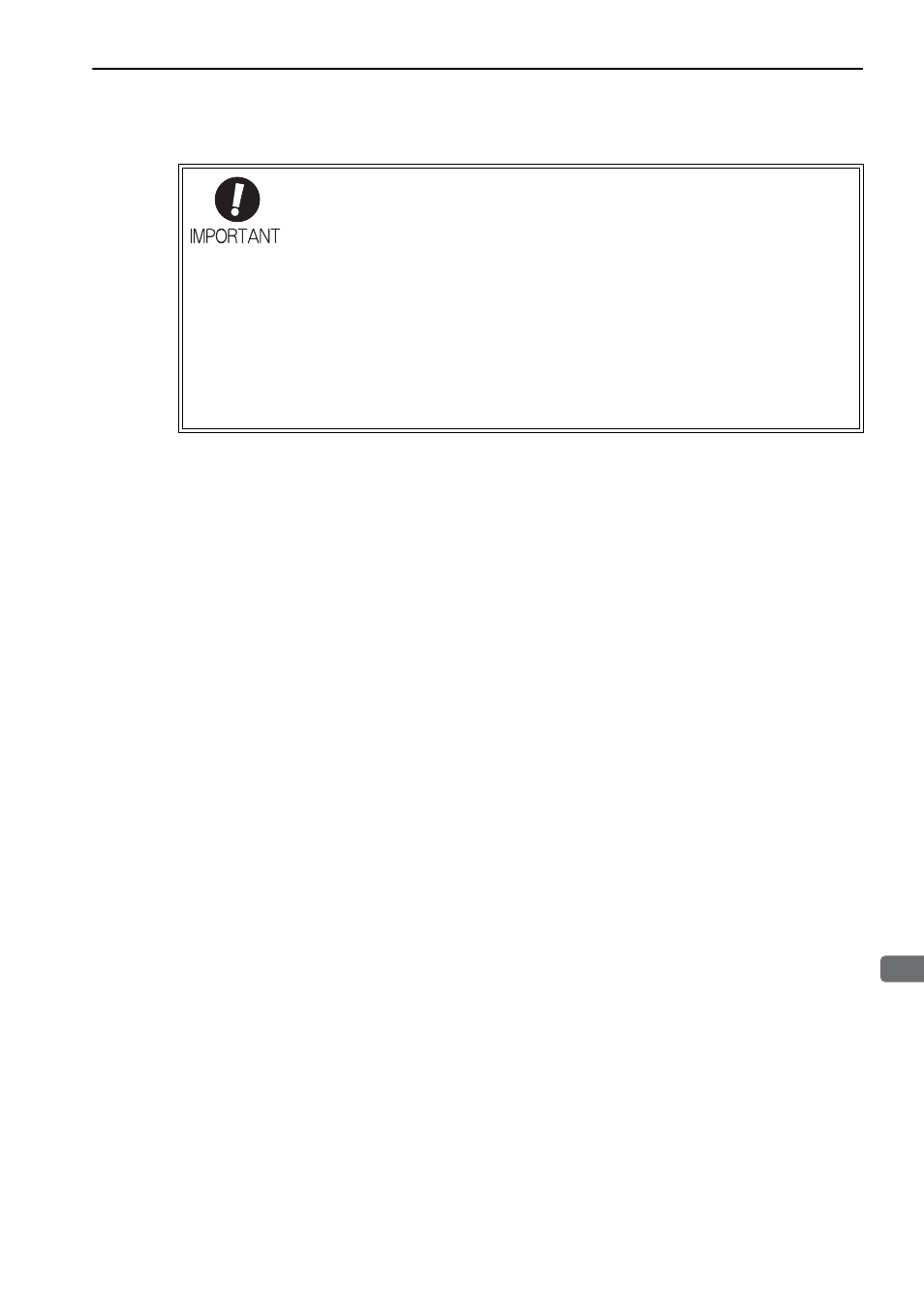
3.1 Main Circuit Wiring
3-7
3
Wirin
g and
Co
nnectio
n
3.1.7
General Precautions for Wiring
To ensure safe, stable application of the servo system, observe the following precautions when wiring.
• Use the connection cables specified in
Σ
-V Series Product Catalog
(Catalog No.: KAEP S800000 42).
Design and arrange the system so that each cable will be as short as possible.
• Use shielded twisted-pair cables or screened unshielded twisted-pair cables for I/O signal cables and
encoder cables.
• The maximum wiring length is 3 m for I/O signal cables, 50 m for servomotor main circuit cables and
encoder cables, and 10 m for power supply cables.
• Observe the following precautions when wiring the ground.
• Use a cable as thick as possible.
• Ground to a ground resistance of 100
Ω
or less.
• Be sure to ground at only one point.
• Ground the servomotor directly if the servomotor is insulated from the machine.
• The signal cable conductors are as thin as 0.2 mm
2
or 0.3 mm
2
. Do not impose excessive bending force or
tension.
• Always use a molded-case circuit breaker (1QF) or a fuse to protect the servo system
from intersystem faults.
• Install a ground fault detector.
The SERVOPACK does not have a built-in protective circuit for grounding.
To configure a safer system, install a ground fault detector against overloads and
short-circuiting, or install a ground fault detector combined with a molded-case circuit
breaker.
• Do not turn the power ON and OFF more than necessary.
• Do not use the SERVOPACK for applications that require the power to turn ON and
OFF frequently. Such applications will cause elements in the SERVOPACK to dete-
riorate.
• As a guideline, at least one hour should be allowed between the power being
turned ON and OFF once actual operation has been started.